Major Challenges in Traditional Drilling Methods
Traditional drilling methods have long been the backbone of oil and gas exploration, but they are not without their challenges. One major issue is the slow rate of penetration when using conventional drill bits, leading to extended drilling times and increased costs. Additionally, the lack of precision in steering the drill bit can result in deviations from the desired well path, causing inefficiencies and potentially compromising the integrity of the wellbore.
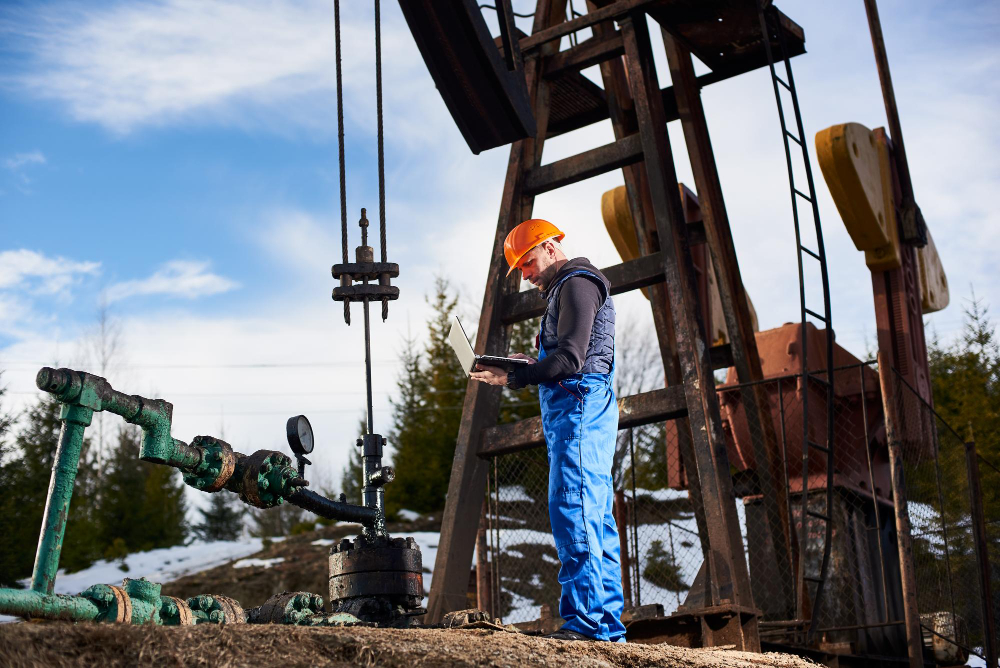
Another significant challenge for traditional drilling methods is the limitations in real-time data monitoring and analysis. Without advanced measurement while drilling (MWD) technology, operators have limited visibility into downhole conditions, making it difficult to optimize drilling parameters and make informed decisions promptly. This can increase the risk of encountering geological hazards or unexpected formations, leading to costly delays and potential safety issues.
The Evolution of Drill Bits
Drill bits have undergone significant advancements over the years, revolutionizing the drilling industry. Initially, drill bits were simple tools made of sharpened steel that were rotated manually or using primitive drilling rigs. As the demand for drilling deeper and more complex wells grew, the need for more efficient and durable drill bits became apparent. This led to the development of rotary bits with cutter teeth, which greatly improved drilling efficiency and speed.
The evolution of drill bits continued with the introduction of roller cone bits, which had three cones with teeth that could withstand higher temperatures and pressures. These bits enhanced drilling performance in challenging formations, allowing for faster penetration rates and longer bit life. As technology progressed, polycrystalline diamond compact (PDC) bits emerged, offering even greater durability and efficiency in drilling hard rock formations. PDC bits revolutionized the industry with their ability to maintain stability in high-speed drilling operations, marking a significant milestone in the evolution of drill bits.
Innovations in Directional Drilling
Directional drilling has witnessed significant innovations in recent years, allowing for more precise and controlled drilling operations. One of the key advancements is the development of rotary steerable systems, which provide real-time steering capabilities and increased efficiency in navigating complex well trajectories. These systems offer greater flexibility compared to traditional motor-based steering methods, allowing operators to optimize wellbore placement and reach specific targets with improved accuracy.
Another notable innovation in directional drilling is the integration of electromagnetic telemetry technology, which enables operators to transmit data wirelessly between the downhole tools and surface equipment. This technology has revolutionized communication in drilling operations, enhancing data transmission speed and accuracy. By utilizing electromagnetic telemetry, operators can make critical decisions in real time, leading to more precise wellbore placement and improved overall drilling performance.
Enhancements in Measurement While Drilling (MWD) Technology
In the realm of drilling technology, continuous advancements in Measurement While Drilling (MWD) technology have revolutionized the way data is gathered during drilling operations. MWD systems enable real-time monitoring of crucial drilling parameters such as wellbore trajectory, formation properties, and drilling tool performance. By providing accurate and instantaneous data transmission to the surface, MWD technology allows drillers to make informed decisions promptly, enhancing overall drilling efficiency and safety.
Moreover, recent enhancements in MWD technology have focused on improving the reliability and accuracy of downhole measurements. These advancements include better sensors, increased data transmission rates, and enhanced downhole tools that can withstand harsh drilling environments. As a result, drilling operators can now access a wealth of data to optimize drilling processes, minimize downtime, and maximize well productivity. The continuous evolution of MWD technology represents a significant milestone in the drilling industry, paving the way for more efficient and cost-effective drilling operations.
The Rise of Automated Drilling Systems
Automation is revolutionizing the oil and gas industry, particularly in drilling operations. Automated drilling systems are increasingly being adopted to improve efficiency, accuracy, and safety during the drilling process. These systems utilize advanced technology to control various aspects of drilling, such as wellbore trajectory, weight on bit, and drilling parameters, without the need for constant human intervention.
One of the key benefits of automated drilling systems is the ability to optimize drilling performance in real-time. By utilizing algorithms and sensors, these systems can make instant adjustments to drilling parameters based on subsurface conditions, ultimately leading to enhanced productivity and cost-effectiveness. Additionally, automation reduces the risk of human error and improves overall drilling accuracy, making it a valuable tool for modern drilling operations.
Improvements in Real-Time Data Analysis
Real-time data analysis in drilling operations has seen significant improvements in recent years. With the advancement of sensor technology and data processing algorithms, companies are now able to gather, analyze, and interpret data faster and more accurately than ever before. This real-time data analysis allows drillers to make informed decisions quickly, leading to more efficient and cost-effective drilling processes.
Furthermore, the integration of artificial intelligence and machine learning techniques has revolutionized how real-time data is utilized in drilling operations. These technologies enable predictive analytics, allowing drillers to anticipate potential issues and make proactive adjustments to optimize drilling performance. By harnessing the power of real-time data analysis, drilling companies can improve safety, increase productivity, and maximize the success of their drilling projects.
Advancements in Drilling Fluids and Mud Systems
Advancements in drilling fluids and mud systems have been pivotal in improving the efficiency and safety of drilling operations. The development of innovative additives and formulations has enabled better control of wellbore stability and pressure while reducing friction and preventing formation damage. These advancements have also played a key role in enhancing the overall performance and longevity of drilling equipment, ultimately leading to cost savings and increased productivity in the industry.
Furthermore, the continuous research and implementation of environmentally friendly drilling fluids have been a significant focus in recent years. With the growing emphasis on sustainability and environmental responsibility, the use of biodegradable and non-toxic fluids has become increasingly prevalent. These eco-friendly options not only minimize the impact on surrounding ecosystems but also comply with strict regulations, demonstrating a commitment to sustainable drilling practices.
The Role of Robotics in Drilling Operations
Robotics plays a crucial role in modern drilling operations, revolutionizing the way tasks are carried out in the oil and gas industry. Robots are being utilized to perform a wide range of duties that are often considered monotonous, dangerous, or challenging for human workers. These automated systems can handle repetitive tasks with precision and efficiency, minimizing the risk of errors and accidents in the drilling process.
One of the key advantages of using robotics in drilling operations is the ability to access remote or hazardous locations with ease. By deploying robots in these environments, operators can improve safety measures and minimize human exposure to dangerous situations. Additionally, robotic systems can enhance data collection and analysis capabilities, providing real-time insights that help optimize drilling performance and decision-making processes.
Technological Breakthroughs in Wellbore Stability
Drilling operations encounter various challenges related to wellbore stability, with issues such as wellbore collapse, hole enlargement, and formation damage posing risks to overall efficiency and safety. To address these concerns, technological breakthroughs in wellbore stability have played a pivotal role in enhancing drilling practices. Innovations in downhole tools and equipment have enabled better monitoring and control of wellbore conditions, leading to improved stability and reduced drilling risks.
One key advancement in wellbore stability technology is the development of real-time monitoring systems that provide immediate feedback on formation pressures, temperatures, and rock properties. By utilizing sensor technologies and data analytics, drilling engineers can make informed decisions to optimize drilling parameters and mitigate stability issues. Additionally, the integration of artificial intelligence and machine learning algorithms has enabled predictive modeling of wellbore behavior, allowing for proactive measures to maintain stability throughout the drilling process.
The Impact of 3D Seismic Imaging on Drilling Efficiency
3D seismic imaging has revolutionized the way drilling operations are conducted in the oil and gas industry. By providing a detailed view of subsurface formations, this technology enables operators to better understand the geology and make more informed decisions when planning wells. The high-resolution images generated through 3D seismic surveys help identify potential reservoirs, fault lines, and other geological features that can impact drilling efficiency and success.
Moreover, 3D seismic imaging plays a crucial role in reducing drilling risks and optimizing well placement. By accurately mapping the subsurface structure, operators can plan well trajectories more effectively, avoiding hazards such as faults and unstable formations. This leads to increased drilling efficiency, faster operations, and ultimately, improved production rates. The integration of 3D seismic data with drilling technologies has significantly enhanced the overall success and cost-effectiveness of drilling projects, making it a valuable tool in the modern oil and gas industry.
Advances in Managed Pressure Drilling (MPD)
Managed Pressure Drilling (MPD) has revolutionized the oil and gas industry by offering a more efficient and safer approach to drilling operations. By precisely controlling the wellbore pressure, MPD mitigates the risks associated with drilling in challenging conditions such as narrow pressure windows or unstable formations. This method allows for optimal wellbore stability and minimizes the likelihood of kicks and blowouts, providing a more controlled drilling environment.
Furthermore, MPD enables operators to maximize drilling efficiency and reduce non-productive time by continuously monitoring downhole pressure conditions and adjusting drilling parameters in real-time. This proactive approach to well control not only enhances safety but also boosts overall drilling performance, leading to faster drilling rates and improved wellbore quality. As the industry continues to embrace MPD technology, we can expect to see further advancements in drilling techniques and increased operational success in complex drilling scenarios.
The Future of Drilling Technology: Predictive Analytics
With the rapid advancements in data analytics and machine learning, the future of drilling technology is set to be revolutionized by predictive analytics. By harnessing the power of predictive algorithms, drilling operators can anticipate operational issues before they occur, leading to improved decision-making and increased efficiency. This shift towards predictive analytics in drilling operations holds the potential to significantly reduce downtime, enhance safety measures, and optimize overall performance.
Through real-time monitoring and analysis of various drilling parameters, predictive analytics can provide valuable insights into wellbore conditions and equipment health. By establishing patterns and trends from historical data, drilling engineers can proactively address potential challenges, resulting in cost savings and enhanced operational productivity. Furthermore, the integration of predictive analytics into drilling technology paves the way for a more data-driven and proactive approach to well construction and production management.
• By utilizing predictive analytics, drilling operators can anticipate equipment failures and prevent costly downtime
• Real-time monitoring of drilling parameters allows for quick adjustments to optimize performance and efficiency
• Predictive algorithms can identify potential hazards in wellbore conditions, improving safety measures
• Historical data analysis enables proactive decision-making to address operational challenges before they escalate
Environmental Considerations in Modern Drilling Practices
Environmental considerations in modern drilling practices have become increasingly important as the industry strives to minimize its impact on the environment. One key focus area is reducing the carbon footprint of drilling operations by implementing more sustainable practices and technologies. This includes utilizing cleaner drilling fluids, optimizing drilling techniques to reduce energy consumption, and implementing proper waste management procedures to mitigate environmental harm.
In addition to reducing carbon emissions, minimizing water usage and protecting water quality are also crucial aspects of modern drilling practices. Techniques such as water recycling and responsible water disposal are being emphasized to ensure that drilling operations do not contaminate freshwater sources or deplete local water supplies. By incorporating environmentally friendly practices into drilling operations, the industry can work towards a more sustainable future while still meeting the demands of global energy needs.
Additional Resources:
[newsletter]
Table of Contents
Categories:
- Additive Manufacturing
- Advanced Equipment
- Asset & Resource Management
- Automation & Robotics
- Big Data & Analytics
- Bio-mining
- Cloud Computing
- Cybersecurity
- Deep Sea Mining
- Digital Transformation
- Emerging Technologies
- Environmental Stewardship
- Geospatial Technologies
- Materials Science
- Mine Planning & Optimization
- Mining 4.0
- Mining Safety
- Ore Processing & Sorting
- Predictive Maintenance
- Satellite & Drone Exploration
- Smart Mining
- Smart Transport Solutions
- Uncategorized
- Wearable & Monitoring Tech
Latest Posts:
FAQs:
What are some major challenges in traditional drilling methods?
Some major challenges in traditional drilling methods include environmental impact, inefficient use of resources, and limitations in reaching specific targets.
How has drill bit technology evolved in modern drilling practices?
Drill bit technology has evolved to include advanced materials, improved designs for better cutting efficiency, and specialized bits for different types of formations.
What are some innovations in directional drilling that have improved efficiency and accuracy?
Innovations in directional drilling include advanced surveying tools, downhole motors for steering, and software for real-time monitoring and control.
How has measurement while drilling (MWD) technology improved in recent years?
MWD technology has improved with the development of more accurate sensors, faster data transmission rates, and enhanced software for data analysis.
What role do automated drilling systems play in modern drilling practices?
Automated drilling systems help improve efficiency, reduce human error, and enable continuous operation without the need for constant manual intervention.
How have drilling fluids and mud systems advanced to be more environmentally friendly?
Drilling fluids and mud systems have advanced with the use of biodegradable additives, improved waste management techniques, and recycling of drilling fluids.
What is the role of robotics in drilling operations?
Robotics are used in drilling operations for tasks such as pipe handling, wellbore cleaning, and equipment maintenance, improving safety and efficiency.
How have technological breakthroughs improved wellbore stability in drilling operations?
Technological breakthroughs have led to better wellbore stability through improved geomechanical modeling, real-time monitoring, and advanced drilling techniques.
How has 3D seismic imaging impacted drilling efficiency?
3D seismic imaging has improved drilling efficiency by providing detailed information about subsurface geology, helping to identify potential drilling targets and reduce risks.
What are some key advances in managed pressure drilling (MPD) technology?
Advances in managed pressure drilling technology include better control systems, improved well control techniques, and increased safety measures to prevent kicks and blowouts.
What is the future of drilling technology in terms of predictive analytics?
The future of drilling technology involves the use of predictive analytics to anticipate drilling challenges, optimize operations, and improve decision-making for more efficient and sustainable practices.